Bau des Wabnaki
- Fritz
- 13. Juni 2015
- 4 Min. Lesezeit
Das erste Holzkanu. Ganz schön viele Unbekannte auf einmal, wenn man sowas vorher noch nie gemacht hat. Zum Glück gibt es Literatur ... wenn auch fast nur amerikanische mit angloamerikanischen Maßen. Glücklicherweise hatten wir bereits jahrelange Erfahrung im Umgang mit Werkzeugen und Materialien, wenn auch noch nie etwas mit Kanus zu tun. Wir kauften uns das Buch "Building a Strip Canoe" von Gil Gilpatrick und entschieden uns für den Entwurf des Wabnaki-Kanadiers. Er ist kurz uns durch den flachen Rumpf sehr wendig, genau richtig zum Paddeln auf der Wupper.

Der Zuschnitt der Leisten erfolgte noch im Dezember 2014. Wir wählten nordische Kiefer, da wir ein helles, europäisches Holz verwenden wollten. Kiefer ist günstig und auch in langen Maßen leicht zu bekommen. Für Süllrand, Sitze, Ducht und Decks wählten wir Esche. Diese passt farblich gut zur Kiefer und ist zäh. Für die geplante Zierleiste wählten wir Merantiholz. Für den Zuschnitt der Leisten bauten wir uns ein temporäres "Sägewerk", da wir vor und hinter der Säge mindestens fünf Meter Platz brauchten. Ca. 12 Meter also, die über die komplette Länge mit Tischen auf Höhe der Tischkreissäge ausgestattet werden müssen. Nach dem Sägen der 6mm starken Holzleisten frästen wir diese noch konkav und konvex mit einem sogenannten Rolladenfräser. So lassen sich die Leisten später lückenlos in jedem erdenklichen Radius verleimen. Nach drei Tagen harter Arbeit für uns, die Säge, die Fräse sowie unsere Staubmasken und Gehörschützer, waren alle Leisten bereit zu einem Holzkanu verarbeitet zu werden. Die Helling stand auf der Agenda an nächster Stelle. Diese sollte möglichst starr und verwindungssteif sein, da darauf das spätere Kanu seine Form annimmt. Zwei starke Konstruktionshölzer übernahmen diese Aufgabe. Ist alles waagerecht ausgerichtet, kann mit dem Bau der Spanten begonnen werden. Wir klebten die Zeichnungen mit Sprühkleber auf Spanplatten und sägten diese grob mit der Stichsäge aus. Mit dem Bandschleifer wurde die Form exakt auf die Linie heruntergeschliffen. Das Befestigen und Ausrichten der Spanten auf der Helling ist ein Schritt, für den man sichZeit nehmen sollte, da dieser die spätere Form des Holzkanus bestimmt. Arbeitet man hier ungenau, kann es zu unsymmetrischen Rumpfformen kommen. Die erste Leiste anzubringen bringt einen motivationstechnisch weit voran. Man hat nun nach tagelanger Arbeit das erste Stück Holz angebracht, das später auch wirklich zum Kanu gehört. Da wir das Boot ohne Tacker bauen wollten, fixierten wir die Leisten während der Leim trocknete mit dafür zugesägten Winkeln aus Spanplatte, die wir mit Zwingen an den Spanten befestigten. Begonnen wird mit der Beplankung am Süllrand des Kanus (also praktisch oben). Die ersten Leisten sind schnell angebracht, jedoch wird die Arbeit an den Radien des Rumpfes zunehmend schwieriger. Die Leisten müssen hier in Sich verwunden werden, was das in Form bringen und verleimen erschwert. Hat man sich schließlich um diese Radien herumgearbeitet, beginnt sich der Rumpf zu schließen. Die Leisten müssen nun aufwändig mit dem Hobel millimetergenau angepasst werden, um das ovale Loch im Rumpf zu schließen. Die letzte Leiste findet ihren Platz an der Kiellinie und wird traditionell mit einem Whiskey begossen.
Schleifen hat noch niemandem so richtig Spass gemacht (wir können uns das jedanfalls nicht vorstellen), jedoch führt beim Leistenkanubau nichts drumrum. Die Außenseite des Rumpfes ist dank Exzenterschleifer jedoch schnell erledigt. Danach kurz anfeuchten, damit sich die Holzfasern aufstellen, nochmal ein kurzer Handschliff mit 120er Papier und die Außenseite ist fertig zum ...
Laminieren. So nennt man den Prozess des Aufbringens von GFK, also Glasfaserverstärktem Kunststoff. Eine Lage Glasfasergewebe wird mit glasklarem zweikomponentigem Epoxidharz getränkt. Das weisse Glasgewebe wird dadurch transparent und gibt die Sicht auf das schöne Holz frei. Die Glasfasern bestimmen maßgeblich die Stabilität des dünnen Holzrumpfes. Da Epoxidharz chemisch nicht ganz ungefährlich ist, arbeiten wir mit Gasmaske, Nitrilhandschuhen und Overall. Laminiert wird nass in nass in mehreren dünnen Schichten. Wann die vorige Schicht bereit ist für die nächste hängt von der Temperatur ab. Durch die Verwendung eines Harzes mit langer Topfzeit dehnt sich dieser Arbeitsschritt zwangsläufig auf die Nacht aus. Nach zwei bis drei "Fillcoats" darf die GFK-Schicht aushärten. Nun kann der Rumpf das erste mal von der Helling gehoben werden. Man hält nun zum ersten mal eine Art Kanu in den Händen und bekommt ein Gespür für sein späteres Gewicht. Es folgt der Schliff der Innenseite (viel Handarbeit) und die Laminierung (natürlich wieder mit Nachtschicht). Die Wegerleisten können nun angebracht werden. Die bereits zugesägten Eschenleisten werden mit Epoxidharz verklebt und mit einer Vielzahl von Zwingen an Ort und Stelle gehalten. An ihnen werden später die Sitze, Decks sowie die Ducht befestigt. Außerdem tragen sie zur Stabilität des Rumpfes bei. Schleifen, mal wieder. Man ist es ja schon gewohnt. Nun muss noch einmal der komplette Rumpf vor der endgültigen Lackierung geschliffen werden. Eine Maschine wäre hier die falsche Wahl, da man schnell ins Gewebe schleifen würde und die Fasern so wieder sichtbar würden. Nach dem Einbau der Sitze, Decks und Ducht kann die abschließende Lackierung aufgebracht werden, die das Holz vor Verrottung und das Epoxidharz vor UV-Strahlung schützt. Nach einigen Schichten Klarlack kann das Holzkanu genutzt werden.
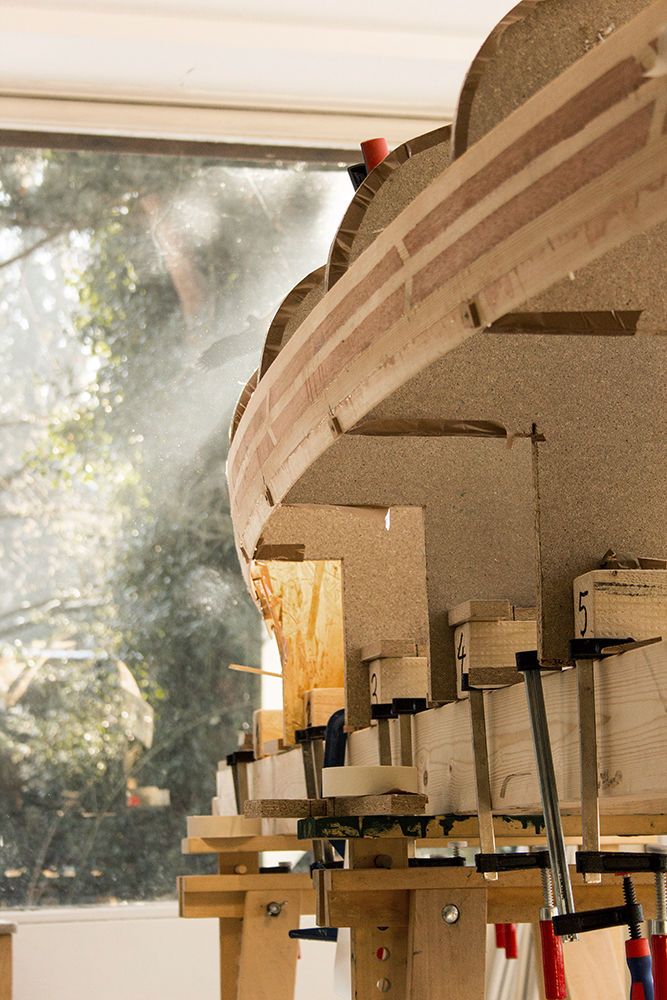
Comments